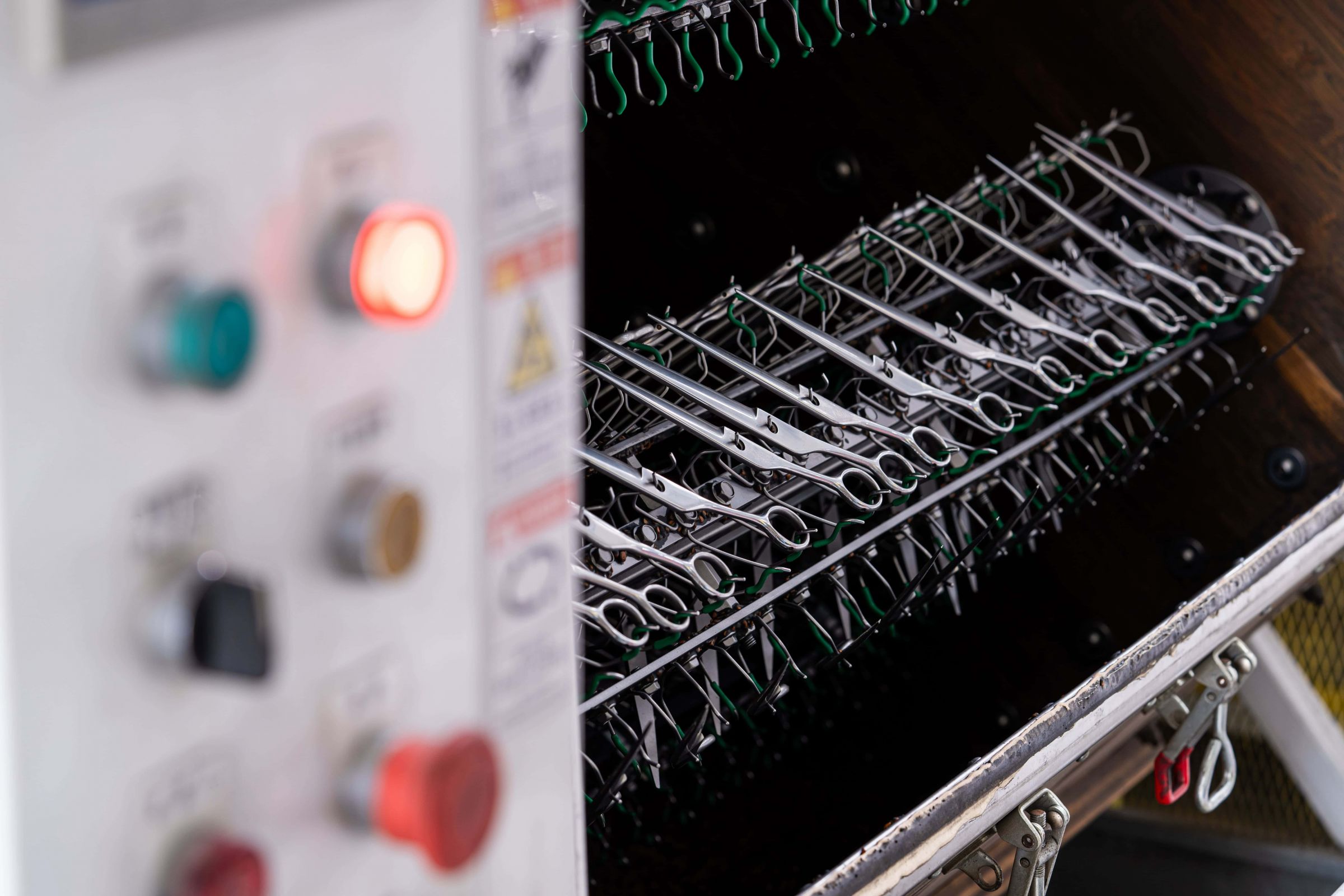
Production Processes
The production of Eversharp scissors is more than just a series of steps; it's a testament to uncompromising dedication and masterful craftsmanship. From the careful selection of premium Japanese stainless steel to the intricate processes of stamping, heat treatment, CNC grinding, beveling, and beyond, every stage reflects our relentless pursuit of excellence. We firmly believe that only through meticulous attention to detail can we create truly exceptional scissors that offer users a sharp, durable, and comfortable experience. Eversharp scissors are not merely tools; they are the perfect embodiment of the artisan spirit
Production Workflow
Stainless Steel Stamping
Stainless steel stamping is a critical step essential for crafting high-quality scissors. Our process begins with selecting premium Japanese stainless steel sheets, which are then processed to form the intricate blades and handles of scissors. Whether for professional use or everyday tasks at home, Eversharp stainless steel stamped scissors offer the best quality shears on the market.
Heat Treatment
Heat treatment is essential for improving scissors' performance and durability. By heating the blades to specific temperatures and cooling them at controlled rates, we refine the metal's grain structure, enhancing hardness, toughness, and strength. This process also reduces internal stresses and improves wear resistance, ensuring sharp edges and durability.
Hollow Grinding by CNC
CNC hollow grinding is a precise method for enhancing scissors' sharpness and cutting efficiency. It automates the grinding of concave surfaces along the blade, creating a hollow grind that improves edge precision. CNC ensures consistent geometry, maintaining uniform thickness and alignment. The result is scissors with superior cutting performance, reduced friction, and better maneuverability.
Scissor Cleaning and Oiling
After assembly, scissors are cleaned and oiled to ensure optimal performance and longevity. This process removes debris, enhances blade clarity, and applies a protective layer to prevent rust and maintain sharpness. It is essential for professional scissors used in hairdressing, sewing, and crafting, ensuring precision and durability.